Como fazer um plano de manutenção?
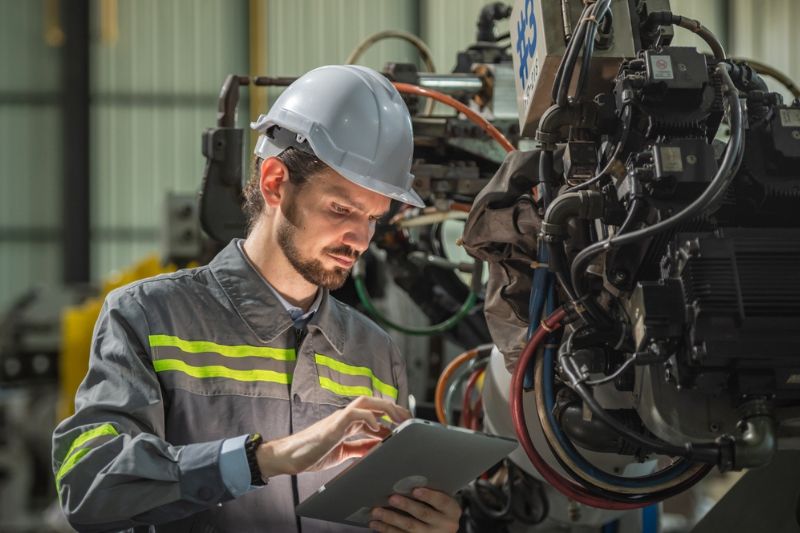
O plano de manutenção auxilia no gerenciamento dos ativos, definindo a frequência correta para os seus ajustes e inspeções. As máquinas são peças-chave da produção e o seu bom desempenho depende de um acompanhamento adequado, papel executado pelo plano de manutenção. Saiba como fazer esse planejamento na sua empresa!
O plano de manutenção é um mapeamento que identifica, dentre outras coisas, a necessidade de reparo em máquinas e equipamentos, a periodicidade desses ajustes e as atividades que serão executadas.
Trata-se de um cronograma que organiza as manutenções e direciona a equipe responsável, ajudando a empresa a ter um controle maior sobre os serviços necessários para o desempenho contínuo das operações industriais.
Os objetivos do plano de manutenção são muitos e incluem: maximizar a vida útil dos equipamentos, minimizar as paradas não programadas, evitar a ociosidade de trabalhadores, garantir maior segurança operacional e reduzir custos.
O plano de manutenção pode ser do tipo preventivo, preditivo e corretivo. Saiba mais sobre cada um deles, a seguir:
O plano de manutenção preventiva é focado na prevenção de problemas. O objetivo é evitar que a máquina deixe de funcionar por alguma falha que poderia ser evitada com a inspeção e com a correção em tempo hábil.
A manutenção preventiva é realizada de forma programada, periodicamente, para garantir que os equipamentos continuem operando com o máximo de desempenho.
Os dispositivos são inspecionados e, durante a avaliação, detalhes importantes são averiguados, como o desgaste das peças, a necessidade de limpeza e a substituição de componentes.
Por ter o objetivo de não pausar a produção, esse procedimento é realizado durante os momentos de menor atividade das máquinas.
A manutenção preventiva é a melhor maneira de prolongar a vida útil dos ativos industriais, uma vez que evita que pequenas falhas se transformem em alterações graves, difíceis de corrigir e que podem comprometer profundamente a máquina em uso.
Leia também: Como evitar a oxidação em máquinas?
A manutenção preditiva acontece de forma recorrente e contínua. A principal diferença em relação ao modelo anterior é que, na preventiva, as inspeções são programadas para momentos específicos.
Já na manutenção preditiva, a manutenção é constante e ocorre por meio da observação dos sinais emitidos pela máquina e que podem indicar problemas diversos, como quebra de peças, baixa lubrificação, desgaste e mau desempenho.
As máquinas são monitoradas e, com a ajuda do operador e do técnico responsável, alguns parâmetros são avaliados, como o nível de vibração, o volume do ruído, a temperatura, a presença de vazamentos e de trincas nas peças.
Assim como a manutenção preventiva, a manutenção preditiva tem o objetivo de evitar as pausas não programadas causadas por problemas que poderiam ter sido evitados se tivessem sido descobertos e corrigidos em sua fase inicial.
Com o monitoramento frequente, as máquinas ganham uma vida útil maior, atuam com mais eficiência e qualidade e, além disso, os reparos e substituições são menos custosos, do ponto de vista financeiro.
A manutenção corretiva é realizada quando o problema já está instalado. A finalidade é solucionar essa ocorrência o mais rápido possível e diminuir o tempo de inatividade da máquina, causada por uma falha inesperada ou negligenciada.
Essa manutenção não é indicada por vários motivos e o principal deles é a pausa forçada dos equipamentos e da equipe de trabalho. A ociosidade interrompe a produtividade e atrapalha a lucratividade do negócio.
A manutenção corretiva também tem um impacto financeiro maior no orçamento da empresa.
Para garantir a continuidade das operações, o gestor precisa corrigir o defeito com urgência. Portanto, ele tem menos tempo disponível para negociar valores e acaba adquirindo peças, dispositivos e serviços por preços muito mais elevados.
A manutenção corretiva representa uma despesa não planejada e compromete a qualidade da produção, impactando na satisfação do consumidor e na imagem da empresa frente ao mercado.
Por isso, a manutenção adequada é aquela que se antecipa ao problema e não a que foca apenas na sua correção.
Leia também: Equipamentos industriais: quais são os tipos e como escolher?
Elaborar um plano de manutenção demanda tempo, dedicação, organização, visão detalhada da empresa, participação da equipe e compromisso na execução daquilo que foi programado. Podemos dividir esse processo em fases. Conheça quais são:
A primeira fase da criação de um plano de manutenção é o mapeamento das máquinas da empresa. Esse é o momento de identificar todas elas, localizá-las e listar características importantes, como o histórico de falhas e os principais problemas encontrados.
Nessa etapa, que também pode ser chamada de inventário, devem ser destacados outros pontos importantes, como a data de fabricação e de aquisição do equipamento, o nome do fabricante, o modelo e seu número de identificação.
A coleta de dados é essencial para garantir que nenhuma máquina fique de fora do cronograma de avaliação.
O próximo passo é listar as máquinas que requerem manutenção, seja para solucionar problemas já apresentados ou para evitar que eles surjam inesperadamente.
Na sequência, deve ser estabelecido o intervalo entre as intervenções, é preciso levar em conta o fluxo de produção e os períodos de pausas.
Outra medida importante é estabelecer o nível de criticidade dos ativos. Ele é definido pelo impacto que uma máquina possui no processo de produção ou na segurança dos trabalhadores.
As máquinas consideradas mais críticas são aquelas que, em caso de falha, podem causar acidentes graves ou podem parar toda a sequência de produção. Logo, elas merecem mais atenção durante a inspeção.
O próximo passo é registrar as peças e componentes que sofrem mais desgaste e que precisam ser recuperados com uma maior frequência. Essa estratégia auxilia na compra de peças por valores mais acessíveis, uma vez que serão adquiridas em grandes quantidades.
A terceira fase da elaboração do plano de manutenção é a definição das atividades a serem realizadas. Alguns procedimentos podem ser urgentes, para sanar problemas atuais, e outros serão programados.
Além da definição das tarefas, esse é o momento de delegar funções. Aqui, deve ser definido o nome do profissional responsável pela execução dos serviços, pela supervisão do trabalho e pelo registro das informações nos sistemas de controle.
Os prazos também devem estar fixados no cronograma para a verificação do cumprimento das tarefas atribuídas a cada colaborador.
Atividades e executores definidos, chegou a hora de selecionar as ferramentas de execução. Além delas, os dispositivos de controle, os sistemas de gerenciamento e outros mecanismos importantes para o processo também devem ser indicados.
Esse é o momento de captar e alocar recursos, distribuindo-os corretamente, além de investir em treinamento da equipe, de acordo com as atribuições de cada membro.
O passo seguinte é a aquisição das ferramentas e peças necessárias. A Imdepa disponibiliza um catálogo diversificado de peças para manutenção de equipamentos industriais.
Após a distribuição de recursos, treinamento de funcionários e aquisição dos instrumentos de trabalho, é hora de iniciar o cronograma e executar o plano.
É a hora de colocar em prática o que foi planejado. Algumas urgências que forem surgindo ao longo do tempo serão ajustadas conforme a necessidade.
O processo de manutenção exige a participação ativa de toda a equipe de trabalho, seja na observação das máquinas, na execução das atividades ou na supervisão dos demais envolvidos.
O engajamento da empresa é imprescindível para o sucesso do projeto e pode ser acompanhado pela última etapa do plano, que é o controle e o monitoramento do processo.
O controle acompanha todo o processo de construção do plano de manutenção, mas é ainda mais necessário na fase de implementação. O objetivo é verificar se os objetivos estão sendo alcançados para, a partir daí, fazer os ajustes necessários.
Quando o plano de manutenção se mostra, de fato, eficiente, ele oferece benefícios diversos para a empresa, funcionários, fornecedores e consumidores. Conheça algumas dessas vantagens:
O plano de manutenção preventiva e preditiva evita paradas não programadas. Essas interrupções repentinas inviabilizam o fluxo de produção, impedem o cumprimento dos prazos e frustram os clientes que aguardam, ansiosos, os seus produtos.
Embora seja preciso pausar as operações durante as manutenções preventivas e preditivas, essa inatividade dura pouco tempo, pois nessas ocasiões, os ajustes são mais simples e rápidos, e as pausas são decididas de forma estratégica.
O plano de manutenção também prolonga a vida útil dos ativos, uma vez que eles estão em constante processo de monitoramento para que não apresentem falhas mais graves.
Todos esses fatores reduzem os custos envolvidos na aquisição de peças, na substituição de equipamentos, na contratação de serviços especializados e no desperdício de matéria-prima.
Equipamentos em bom estado de conservação e com funcionamento regular são menos propensos a causar acidentes de trabalho. Portanto, além de prolongar a vida útil das máquinas, o plano de manutenção também assegura a integridade física dos colaboradores.
De acordo com o Tribunal Superior do Trabalho (TST), a cada quatro horas, um trabalhador perde a vida em um acidente de trabalho. As ocorrências mais comuns incluem cortes, lacerações, fraturas e esmagamentos.
Ainda de acordo com o órgão, a precarização das condições de trabalho e a falta de medidas coletivas de segurança são fatores que contribuem para o alto número de acidentes.
Investir na melhoria das máquinas industriais, assegurar a disponibilidade de equipamentos de proteção individual para a equipe e aplicar as normas de segurança relacionadas são práticas necessárias e devem fazer parte do plano de manutenção da organização.
A melhoria na qualidade dos produtos fabricados é um dos benefícios mais vantajosos, pois repercute na imagem da empresa no mercado e interfere na satisfação do seu consumidor final.
O controle de qualidade também depende do desempenho das máquinas industriais. A manutenção adequada, feita da forma correta e no prazo ideal, garante a produção dentro dos padrões estabelecidos pela indústria.
Com isso, temos produtos menos suscetíveis a defeitos, menos desperdício de matéria-prima, eficiência da produção, redução de custos e garantia de satisfação do cliente.
Máquinas defeituosas têm baixo desempenho e consomem muito mais energia elétrica para executar as tarefas para as quais estão programadas. O plano de manutenção corrige essas falhas, faz substituições e promove um chão de fábrica muito mais ágil, produtivo e eficiente.
Leia também: Saiba quais são as principais peças para indústria
Ao longo do tempo, a indústria tem experimentado uma modernização contínua de seus processos e equipamentos. Essa evolução também chegou na manutenção de ativos, que incorporou alguns métodos modernos em sua execução. Conheça algumas dessas tendências:
A manutenção autônoma se destaca pelo uso de softwares e ferramentas de automação que tornam a implementação do plano de manutenção muito mais simples de ser cumprida.
Com as estratégias adotadas, é possível, por exemplo, agendar inspeções e emitir alertas no dia marcado para que a atividade não seja esquecida. Com isso, fica mais fácil cumprir os prazos e alcançar os objetivos.
A inteligência artificial utiliza sensores para coletar e transmitir dados. Essa funcionalidade permite o monitoramento remoto dos ativos, reduz o contato humano com essas atividades e aumenta a segurança dos processos.
A manutenção por condição é realizada conforme os resultados obtidos durante o monitoramento das máquinas.
É uma tendência que também está relacionada à aplicação de recursos de inteligência artificial, como a IoT e o machine learning, metodologias que conferem às máquinas habilidades humanas.
Essas e outras tecnologias estão sendo adotadas nos planos de manutenção atuais e têm aperfeiçoado a sua execução, assegurando muito mais agilidade, segurança e alcance de resultados.
Um bom plano de manutenção faz toda a diferença no desempenho de uma empresa, já que está diretamente relacionado ao processo produtivo. Coloque em prática as nossas dicas e confira as opções de peças industriais disponíveis na loja virtual da IMDEPA.
Categorias: Manutenção